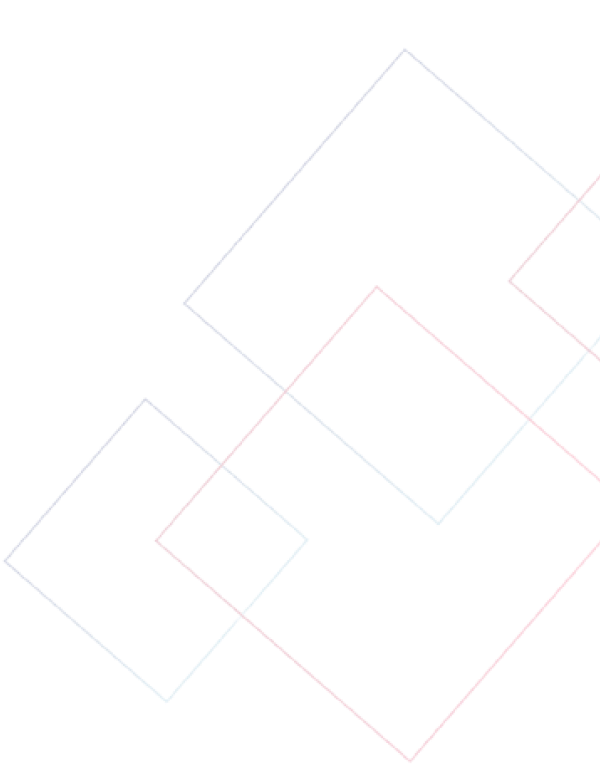
全自動(dòng)封膠線是什么的相關(guān)介紹
時(shí)間:2025-07-18 來源:http://njguanglong.com/ 發(fā)布人:昌盛機(jī)械
全自動(dòng)封膠線是一種集成了供膠、涂膠、壓合、固化等工序的自動(dòng)化設(shè)備,廣泛應(yīng)用于需要密封、粘合工藝的生產(chǎn)環(huán)節(jié),能通過精準(zhǔn)控制實(shí)現(xiàn)物料接縫處的均勻涂膠,大幅提升封膠質(zhì)量與生產(chǎn)效率,減少人工操作帶來的誤差。
The fully automatic sealing line is an automated equipment that integrates processes such as glue supply, coating, pressing, and curing. It is widely used in production processes that require sealing and bonding processes. It can achieve uniform glue coating at material joints through precise control, greatly improving the quality and production efficiency of sealing and reducing errors caused by manual operations.
從結(jié)構(gòu)組成來看,全自動(dòng)封膠線主要由供膠系統(tǒng)、輸送機(jī)構(gòu)、涂膠裝置、壓合組件及固化單元構(gòu)成。供膠系統(tǒng)通過儲膠罐與輸送泵連接,可根據(jù)膠料類型調(diào)節(jié)壓力,確保膠料穩(wěn)定輸出且無氣泡;輸送機(jī)構(gòu)多采用皮帶或鏈條傳動(dòng),通過伺服電機(jī)控制速度,使待封膠工件平穩(wěn)移動(dòng),配合傳感器實(shí)現(xiàn)工件定位。涂膠裝置是核心部分,配備多軸機(jī)械臂或固定噴頭,噴頭口徑可根據(jù)膠線寬度更換,通過程序設(shè)定涂膠路徑,確保膠料均勻覆蓋接縫;部分設(shè)備帶有膠量檢測功能,實(shí)時(shí)監(jiān)控出膠量,若出現(xiàn)斷膠或溢膠,會(huì)自動(dòng)停機(jī)報(bào)警。壓合組件通過氣缸或伺服電機(jī)提供壓力,在涂膠后對工件接縫施加均勻壓力,使膠料與工件表面充分貼合,減少氣泡殘留;固化單元?jiǎng)t根據(jù)膠料特性選擇加熱、紫外線照射或自然固化方式,確保膠層在規(guī)定時(shí)間內(nèi)達(dá)到設(shè)定強(qiáng)度。
From the perspective of structural composition, the fully automatic sealing line is mainly composed of a glue supply system, a conveying mechanism, a glue coating device, a pressing component, and a curing unit. The glue supply system is connected to the conveying pump through a glue storage tank, and the pressure can be adjusted according to the type of glue material to ensure stable output and no bubbles; Conveyor mechanisms often use belt or chain transmission, with servo motors controlling speed to ensure smooth movement of the workpiece to be sealed, and sensors used to achieve workpiece positioning. The glue coating device is the core part, equipped with a multi axis robotic arm or a fixed nozzle. The nozzle diameter can be changed according to the width of the glue line. The glue coating path is set through the program to ensure that the glue material covers the joint evenly; Some devices are equipped with glue quantity detection function, which monitors the glue quantity in real time. If there is a glue breakage or overflow, it will automatically shut down and give an alarm. The compression component provides pressure through a cylinder or servo motor, and applies uniform pressure to the joint of the workpiece after coating, so that the adhesive material fully adheres to the surface of the workpiece and reduces residual bubbles; The curing unit selects heating, ultraviolet irradiation, or natural curing methods based on the characteristics of the adhesive material to ensure that the adhesive layer reaches the set strength within the specified time.
工作流程遵循自動(dòng)化控制邏輯。啟動(dòng)設(shè)備后,操作人員將待加工工件放置在輸送機(jī)構(gòu)的進(jìn)料端,工件隨輸送帶移動(dòng)至定位區(qū),傳感器檢測到工件后發(fā)送信號,輸送機(jī)構(gòu)暫停運(yùn)行。供膠系統(tǒng)開始工作,膠料經(jīng)輸送泵進(jìn)入涂膠裝置,機(jī)械臂或噴頭按預(yù)設(shè)路徑在工件接縫處涂膠,涂膠過程中,膠量檢測裝置同步監(jiān)測,確保膠線連續(xù)、無堆積。涂膠完成后,工件被輸送至壓合區(qū),壓合組件下降并施加壓力,保持一定時(shí)間后復(fù)位。隨后工件進(jìn)入固化單元,通過加熱或紫外線照射加速膠層固化,固化完成后由輸送機(jī)構(gòu)送至出料端,整個(gè)過程無需人工干預(yù),單條生產(chǎn)線每小時(shí)可處理 300-1000 件工件,具體效率取決于工件尺寸與工藝要求。
The workflow follows automated control logic. After starting the equipment, the operator places the workpiece to be processed at the feeding end of the conveyor mechanism. The workpiece moves with the conveyor belt to the positioning area, and the sensor detects the workpiece and sends a signal, causing the conveyor mechanism to pause operation. The glue supply system starts working, and the glue material enters the glue coating device through the conveying pump. The mechanical arm or nozzle applies glue at the joint of the workpiece according to the preset path. During the glue coating process, the glue amount detection device synchronously monitors to ensure that the glue line is continuous and free of accumulation. After the adhesive coating is completed, the workpiece is transported to the pressing area, and the pressing component descends and applies pressure, which is held for a certain period of time before resetting. Subsequently, the workpiece enters the curing unit and is accelerated by heating or ultraviolet irradiation to cure the adhesive layer. After curing is completed, it is transported to the discharge end by a conveying mechanism without manual intervention. A single production line can process 300-1000 workpieces per hour, and the specific efficiency depends on the size of the workpiece and the process requirements.
適用場景覆蓋多個(gè)工業(yè)領(lǐng)域。在汽車制造中,車門與車身的接縫、車窗玻璃安裝處需用全自動(dòng)封膠線涂膠,膠層不僅能實(shí)現(xiàn)密封防水,還能增強(qiáng)結(jié)構(gòu)強(qiáng)度,抵御行駛過程中的振動(dòng)與沖擊;電子設(shè)備生產(chǎn)中,手機(jī)外殼、電池艙的接縫封膠需高精度涂膠,防止灰塵、水汽進(jìn)入內(nèi)部影響元件性能。家具行業(yè)中,實(shí)木板材拼接處通過封膠線涂膠,可避免木材受潮變形,同時(shí)美化接縫外觀;在醫(yī)療器械生產(chǎn)中,無菌設(shè)備的接縫封膠要求膠料無毒、耐消毒,全自動(dòng)封膠線能通過潔凈車間級設(shè)計(jì),滿足醫(yī)療級衛(wèi)生標(biāo)準(zhǔn)。此外,在光伏組件制造中,邊框與玻璃的封膠需耐受高低溫變化,封膠線通過控制膠層厚度與固化條件,確保組件長期使用不出現(xiàn)脫膠。
Applicable scenarios cover multiple industrial fields. In automobile manufacturing, the seams between the car doors and the body, as well as the installation of the window glass, need to be coated with fully automatic sealing lines. The adhesive layer can not only achieve sealing and waterproofing, but also enhance structural strength and resist vibration and impact during driving; In the production of electronic devices, the joint sealing of mobile phone casings and battery compartments requires high-precision coating to prevent dust and moisture from entering the interior and affecting component performance. In the furniture industry, the joints of solid wood panels are coated with glue through sealing lines to prevent moisture and deformation of the wood, while also beautifying the appearance of the joints; In the production of medical devices, the seam sealing of sterile equipment requires that the adhesive material is non-toxic and resistant to disinfection. The fully automatic sealing line can pass the cleanroom level design and meet medical grade hygiene standards. In addition, in the manufacturing of photovoltaic modules, the sealing of the frame and glass needs to withstand high and low temperature changes. The sealing line controls the thickness of the adhesive layer and curing conditions to ensure that the module does not peel off during long-term use.
相比傳統(tǒng)人工封膠,全自動(dòng)封膠線具有顯著優(yōu)勢。封膠質(zhì)量更穩(wěn)定:人工涂膠易出現(xiàn)膠量不均、漏涂等問題,而自動(dòng)封膠線的膠量誤差可控制在合理范圍內(nèi),膠線平整光滑,密封性能提升 30% 以上。生產(chǎn)效率更高:一條全自動(dòng)封膠線的日產(chǎn)量相當(dāng)于 5-8 名熟練工人的工作量,且可 24 小時(shí)連續(xù)運(yùn)行,適合大批量生產(chǎn)。材料利用率提升:通過精準(zhǔn)控制出膠量,減少膠料浪費(fèi),降低生產(chǎn)成本。此外,設(shè)備可通過人機(jī)界面修改參數(shù),快速適配不同工件,切換產(chǎn)品型號時(shí)的調(diào)整時(shí)間大幅縮短,增強(qiáng)生產(chǎn)靈活性。
Compared to traditional manual sealing, fully automatic sealing lines have significant advantages. The sealing quality is more stable: manual glue application is prone to problems such as uneven glue amount and missed coating, while the glue amount error of automatic sealing line can be controlled within a reasonable range, the glue line is flat and smooth, and the sealing performance is improved by more than 30%. Higher production efficiency: The daily output of a fully automatic sealing line is equivalent to the workload of 5-8 skilled workers, and it can operate continuously for 24 hours, suitable for large-scale production. Material utilization rate improvement: By accurately controlling the amount of glue produced, waste of glue is reduced and production costs are lowered. In addition, the device can modify parameters through the human-machine interface, quickly adapt to different workpieces, significantly reduce the adjustment time when switching product models, and enhance production flexibility.
日常操作與維護(hù)需注意以下要點(diǎn)。開機(jī)前需檢查供膠系統(tǒng)是否通暢,膠料是否充足,清理噴頭殘留膠料;運(yùn)行中監(jiān)控設(shè)備各環(huán)節(jié)參數(shù),若出現(xiàn)異響或報(bào)警,應(yīng)立即停機(jī)排查。定期維護(hù)包括清潔輸送機(jī)構(gòu)、更換密封件、校準(zhǔn)機(jī)械臂定位精度。對于易固化的膠料,停機(jī)后需用專用溶劑清洗供膠管路,避免膠料固化堵塞管道,影響下次使用。
Daily operation and maintenance should pay attention to the following points. Before starting up, it is necessary to check whether the glue supply system is unobstructed, whether the glue is sufficient, and clean the residual glue from the nozzle; Monitor the parameters of each link of the equipment during operation. If there is any abnormal noise or alarm, stop the machine immediately for troubleshooting. Regular maintenance includes cleaning the conveying mechanism, replacing seals, and calibrating the positioning accuracy of the robotic arm. For adhesive materials that are easy to cure, it is necessary to clean the adhesive supply pipeline with a special solvent after shutdown to avoid the adhesive material solidifying and blocking the pipeline, which may affect the next use.
本文由全自動(dòng)封膠線友情奉獻(xiàn).更多有關(guān)的知識請點(diǎn)擊:http://njguanglong.com我們將會(huì)對您提出的疑問進(jìn)行詳細(xì)的解答,歡迎您登錄網(wǎng)站留言.
This article is a friendly contribution from glass coating machine equipment For more information, please click: http://njguanglong.com We will provide detailed answers to your questions. You are welcome to log in to our website and leave a message
- 全自動(dòng)封膠線是什么的相關(guān)介紹 2025/07/18
- 中空玻璃加工設(shè)備主要類型及用途 2025/07/16
- 臥式丁基膠涂布機(jī)操作技術(shù)規(guī)范 2025/07/14
- 雙組份打膠機(jī)如何減少堵塞問題 2025/07/11
- 告別繁瑣涂膠,立式丁基膠涂布機(jī)讓效率與精度雙贏 2025/07/10
- 自動(dòng)丁基膠涂布機(jī)與普通的丁基膠涂布機(jī)有什么顯著的差別? 2025/07/09
- 全自動(dòng)封膠線性能上都有什么優(yōu)勢? 2025/07/08
- 臥式丁基膠涂布機(jī)的規(guī)范操作流程 2025/07/07
- 中空玻璃加工設(shè)備:解密 “空氣夾層” 的誕生工廠 2025/07/04
- 雙組份打膠機(jī)的 “呼吸密碼”:解析耗氣量背后的門道 2025/07/03
產(chǎn)品分類Product categories
聯(lián)系我們Contact us
- 咨詢熱線:0531-85717458 13705446998
- 公司地址: 山東省德州市齊河安頭鄉(xiāng)企巢工業(yè)園
- 掃碼聯(lián)系我們: